Ramping it up with PMMA – sealing helix ramps
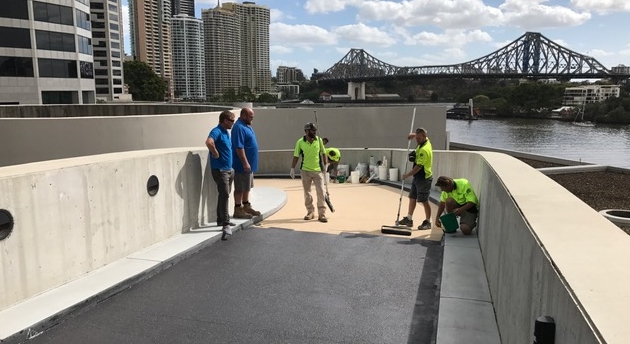
Located in the heart of the Brisbane CBD, the Riverside Centre is one of the city’s most sought after commercial buildings, consisting of 42 levels with 37 tennant floors. In 2016, Hychem products were chosen to seal the helix entry and exit ramps to the connected car park, which has over 500 parking spaces.
Selecting the coating
According to Andrew Bolton, Queensland State Manager at Hychem, Hychem were approached to provide a long-lasting and quick-cure sealing solution.
“The Riverside Centre and its car park are open 24 hours a day, seven days a week, so the client required a product that could be applied and cured with very little downtime to complete the installation,” Mr Bolton said.
“The client also wanted a long-lasting product that would be able to handle the wear and tear of frequent traffic with a minimum ten-year guarantee.
“Hychem’s Polyac BDM – PMMA trafficable membrane system was chosen as it is the best fast curing concrete coating available, as well as being easy to apply and extremely durable.”
A fast cure solution
PMMA based membranes are fast curing, ensuring the coating system can be installed and back in use within hours of installation.
“By selecting a PMMA system, contractors are able to complete large projects and have them ready for service within the same day or night,” Mr Bolton said.
“For the Polyac BDM system, the surface is chemically and mechanically cured, and ready to use again about 60 minutes after the final application of the coating system is installed.
“This was ideal for the client as it not only reduces downtime, and the disruption of the community and losses from parking fees associated with it, but it also provides substantial cost savings through labour savings.”
No compromise
Another advantage of the Polyac BDM PMMA system is that the quality of the product has not been compromised to ensure rapid curing.
“Unlike other coating systems, PMMA systems are able to chemically bond to themselves without the need for aggressive mechanical preparation such as diamond grinding. This means time is saved during surface preparation, and makes re-coating and maintenance quick and easy,” Mr Bolton said.
“PMMA systems are also excellent for use where there is heavy traffic, as they are highly durable and resistant in both high and low temperatures, and are also highly resistant to chemicals such as petroleum which can damage and degrade unprotected concrete.
“They are waterproof with elongation of 300 per cent, making them ideal for outdoor structures such as carparks, bridge decks and terraced areas.
“They are also UV resistant and colour stable. These are particularly important for applications exposed to sunlight where aesthetics is also a concern as UV degrades epoxy resins over time, exposing pigment and causing chalking.”
Applying the coating
Before applying the coating the entry and exit ramps were mechanically prepared by diamond grinding. This ensures the surfaces were free from existing coatings, curing compound, laitance, grease and oil. The concrete was then primed using Polyac 12.
“Once the concrete had been primed two applications of Polyac BDM were applied at 1.5mm. In the final application of Polyac BDM, bauxite was broadcasted to a beach finish, then two pigmented coats of Polyac 61 were used to seal it.
“The project took the team five days to complete the entire project, including preparation and curing, fulfilling the client’s need for minimal downtime.
“The entire project was completed successfully and will protect the ramps well into the future without any degradation of the coating.”