What’s the difference between epoxy, CAC and geopolymer?
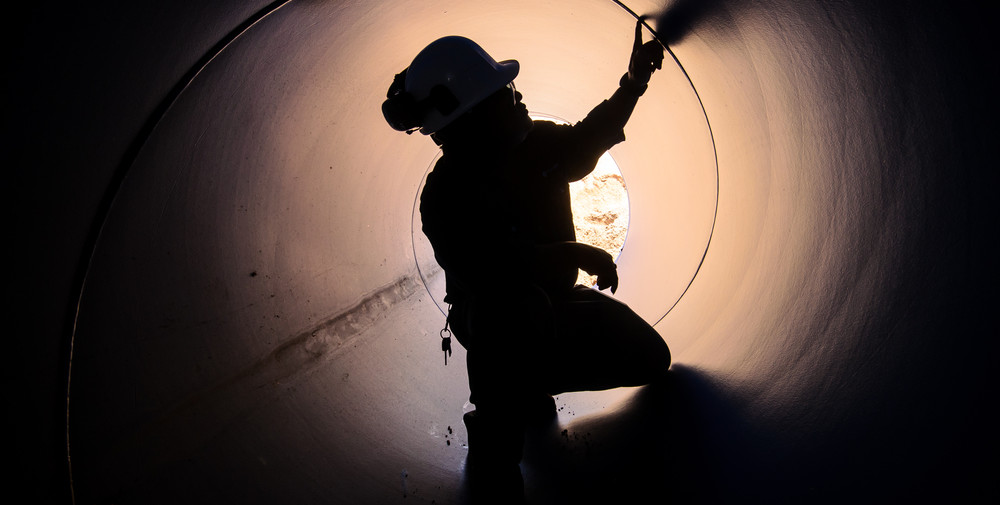
There are two types of coating systems that can be used to protect wastewater infrastructure from microbiologically induced corrosion (MIC): polymers such as epoxy, and concrete based coatings such as calcium aluminate cement (CAC) and geopolymer. Here, we look at epoxy, CAC and geopolymer to help you make better informed decisions when choosing your next coating solution.
Epoxy liners
For the protection and rehabilitation of wastewater infrastructure, epoxy has dominated the market as it has proven to provide long-lasting and durable protection against MIC.
Colin Murphy, Product Manager at Hychem, said epoxy is popular as it is particularly well suited to the task of lining wastewater infrastructure.
“Epoxy offers a number of key benefits for the water industry, including chemical resistance, longevity, low friction and reduced thickness,” Mr Murphy said.
“It has superior acid resistance, which makes it particularly useful in the sewer environment, where structures are subject to acid attack.
“Because it is chemically resistant, epoxy is long lasting and will stay in place with minimal erosion for years and even decades. We have case studies of Hychem’s TL5 showing minimal change 20 years after installation.”
Mr Murphy said another benefit of epoxy is that it has a smooth finish, making it low friction.
“Low-friction coatings are ideal for wastewater infrastructure as it will help prevent blockages from occurring. As matter won’t stick to the liner, it moves through the system.
“Epoxy can also be applied in thicknesses as small as 2-3mm, meaning valuable internal diameter won’t be lost when rehabilitating an asset. In comparison, other liners can have a thickness of up to 30mm+.”
Calcium aluminate cement (CAC)
While not as widely used as epoxy, CAC also provides protection against MIC in wastewater infrastructure and can be used to provide structural integrity to corroding infrastructure.
CAC has a number of key features, including high early strength, low porosity, and high acid neutralisation. It’s high alkalinity also helps to control microbial growth, and curing is enhanced in high humidity or moisture environments.
“Unlike epoxy which is designed to be long lasting and durable, CAC behaves as sacrificial coating where it preferentially corrodes to extend the life of the asset,” Mr Murphy said.
“This means it is more susceptible to corrosion, with the rate of corrosion correlating to the level of hydrogen sulphide the liner in exposed to. So the more hydrogen sulphide, the quicker the coating will deteriorate.”
Rates of corrosion are also expected to increase over time as mineralogical conversion of the CAC to its more reactive phase takes place, resulting in faster corrosion.
In order to achieve extended longevity, CAC needs to be applied at a greater thickness than epoxy with some installations reaching 50mm.
Geopolymer
Geopolymer is a unique formulation using special ingredients, including pozzolans, that react with alkaline to enhance the chemical resistance and physical properties of the mortar. It is used to provide corrosion-resistant protection in high hydrogen sulphide environments, increase structural integrity, and stop the infiltration of groundwater in deteriorated structures.
“Geopolymer can be used for a wider range of applications than CAC. It is suitable for the structural restoration of large diameter pipes (both storm and sewer) consisting of metal, concrete, stone, masonry and others. It can also be used on structures such as manholes, wet wells, and treatment plants, and is suited to structural strength applications,” Mr Murphy said.
“Another benefit of geopolymer is that it has a low-carbon footprint as it is made predominantly of recycled materials which significantly reduces the amount of greenhouse gases typically created in the production of CAC based products.”
Geopolymer also has superior strength and chemical resistance over CACs. In application, Geopolymers offer far superior tenacity and cohesion, this results in far less rebound and wastage in comparison to CAC. In large diameter pipes it is common for Geopolymer to be applied using an automated spinning machine. In the USA, Geopolymer materials have been used in wastewater industry for over 25 years. It is standard practice to specify with a Geopolymer for structural pipe or culvert relining.
Like CAC, geopolymer is applied at a greater thickness than epoxy, with a minimum thickness of around 12mm. A Geopolymer mortar can be applied at thicknesses of 80mm in one pass. The superior physical properties allow it to restore structural integrity to a whole range of pipe shapes and substrate types.